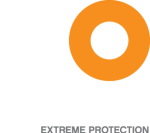
Corex Extreme Protection engineered for cylinders where failure is unthinkable
Do you have a production critical cylinder or a tough environment where standard cylinder solutions just don’t last?
What is Corex?
Corex is a very hard, dense, cohesive hydraulic piston rod coating with extremely high bond strength. It is capable of superb wear and corrosion resistance and help improves cylinder service intervals.
About Corex
Apex have spent 2 years developing Corex through research in the lab and tests in the field. Excellent underground results lead us to offering the solution to our Oil and Gas customers where improvements in performance against standard solutions have been massive. Splash zone cylinders which regularly get dried on seawater or sediment from drilling are particularly successful.
How does Corex improve cylinder durability?
Corex increases resistance to 3 major contributors of ram failure:
- Corrosion
- Wear
- Impact
Improved Corrosion Resistance
Surface coatings work by adding a high corrosion resistant material to the substrate. This locks out the damaging environment increasing life span.
Porosity and cracking in the coating are weaknesses in the defence barrier. If great enough these weaknesses do not open the substrate up to its normal level of corrosion but accelerate it dramatically. This leads to rapid widespread corrosion even in substrates of stainless steel.
Typically the porosity in hard chrome plate (HCP) is between 5% – 10 % while in Corex it is less than 1%
The photo in the below gallery shows the porosity in electroplated hard chrome at 500 times magnification. The black arrow shows a large pore defect and the red arrow shows a through coating crack. Both will lead to rapid corrosion in a marine environment.
Corex Porosity <1%
Improved Wear Resistance
High cycle and side loaded cylinders are particularly susceptible to failure due to wear.
Off the shelf chrome bar can be only a few micron thick and therefore can be quickly worn away.
Not only is the thickness improved with Corex but also hardness and surface finish. Which will reduce the rate of wear. Corex is highly wear resistant and is able to cope with high levels of contamination or fluids with low lubricity such as water.
Extreme Hardness up to 1400 Hv (Microhardness HV0.3) (Macrohardness HR15N > 92)
Wear Rate (ASTM G65 B) < 4.0 mm3 < 0.00061 inch³
Improved Impact Resistance
Failure of a cylinder through external impact is common. This can be by small repeated high velocity impact which erodes HCP leaving the substrate exposed to corrosion or by a single large impact. Large impacts will dent the substrate which will lead to cracking or peeling of coatings. Corex is very dense which greatly improve resistance to small high velocity impacts, while its excellent bond strength ensure a large impact will not cause cracking or peeling.
Extreme Hardness up to 1400 Hv
Excellent Bond Strength > 10,000 psi
Hard Chrome replacement
Electroplated hard chrome has been the standard solution in the hydraulics industry for many years. It offers good all round performance but in corrosive environments and high cycle applications it is usually the first part of the ram to fail. Hexavalent chromium is produced during the electroplating process which is a known carcinogen and harmful to the environment. So not only can you improve cylinder performance you can help reduce a harmful pollutant too.
If you have a production critical cylinder or a tough environment where standard cylinder solutions just don’t last then contact us and we’ll tell you how Corex will help.
We have sector specific solutions for the mining, offshore, subsea, recycling, Rail and the steel production sectors.
Gallery
Please find related images below…
Related Case Studies for COREX
Read more about our experience with COREX within the case studies below
Related Sector Experience for COREX
Read more about our sector experience associated with COREX below
Latest News
Read more about our latest news below